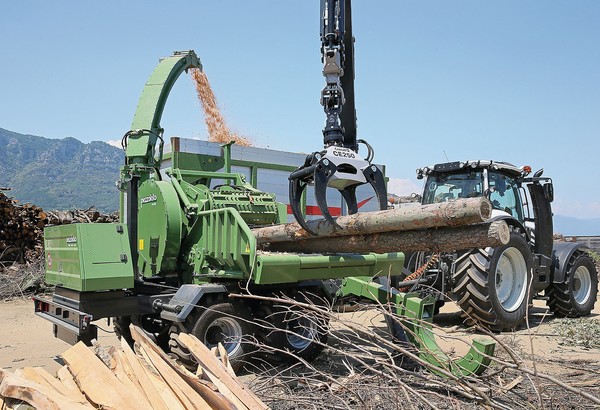
Chippers for every specific requirement
The broad versatility of modern chippers enables them to be profitably used in different work contexts, in all cases, with high productivity and excellent product quality
Aimed at the valorization for energy purposes of woody biomass, chipping seeks to chop the material into smaller-sized flakes (also called "chips"), with some management and process efficiency advantages, such as a tangible optimization of the volume of product compared to wood as such (in sections or logs). It also has the advantage of being able to usefully exploit by-products from different supply chains, such as pruning residues, forestry offcuts or urban greenery, instead of managing them as mere "waste," with the associated operating costs for their disposal.
As a matter of fact, wood chips are ideal for fueling cogeneration power plants which produce electricity and thermal energy simultaneously, gasification establishments and small- to medium-sized boilers. The flake conformation facilitates a continuous and homogeneous type of material loading, while its use in combustion results in the abatement of the use of fossil fuels.
The chipper
This machine is fairly widespread, given also the considerable market offer, from the simplest models with limited working capacity, often suitable for hobby-type realities, to those of large size, used at the professional level. In the latter case, chippers differ in the energy source: numerous models are driven via the tractor's PTO but also equipped with an autonomous motor (endothermic or electric), sometimes mounted on trucks for the machine's better mobility. Chopping machines to be coupled to the tractor can be connected to the three-point hitch or towed and have power requirements ranging from 60-70 to 200-250 Hp. Logically, the maximum diameter of the input material also varies from 30-40 to 60-80 cm, respectively. For larger diameters, models with self-contained engines up to 700-1,000 Hp are used to process pieces up to 800-900 mm in diameter. Truck-mounted chippers are obviously more suitable for road travel (up to 80 km/h) in high capacity settings, up to 400 m³/h.
Electrically powered models obviously feature less noise and lower pollutant emissions, and typically have powers between 50 and 200 kW, capable of processing timber up to 250-450 mm in diameter. Again, on the subject, Pezzolato offers the PTH 1000, with a 200 kW electric motor, which can process logs up to 450 mm in diameter automatically and up to as much as 600 mm with a dedicated operator. Equipped with a drum-cutting device, it has a wide 100-cm inlet for productivity up to 200 m³/h, more than satisfactory for the common needs of biomass power plants and sawmills.
Mode of operation
The material to be chipped is conveyed to the feeding mouth by crane arms, stand-alone or components of the chipper itself. Biomass feed to the chopping rotor is either by gravity, after loading into a hopper, or horizontally, especially for large chunks. In this case, the material feed is carried out by rollers with rubber belts, chain conveyors and channels or vibrating tables.
The cutting apparatus adopted on the high-productivity machinery consists of a drum with staggered sections, equipped with a set of knives, a counter-knife and a sizing grid. The whole allows for clean cuts without harmful mechanical stresses. The length of the flakes is a function of the distance (adjustable within a given range) between the knives and the counter-knife.
To avoid damage to the shredding system, it is advisable to install a metal detector upstream of the drum that detects the presence of foreign ferrous materials and promptly provides a feed block for their removal. In addition, overload protection devices, represented by shear bolts installed on the counter-knife, are now commonly present; if the breakage threshold is exceeded (usually by shear), the counter-knife will move, facilitating the release of material and preventing any damage to the chopping system.
To avoid overloading of biomass input, it is increasingly common to install the "no-stress" (see box), a hydraulic device that modulates the forward speed to the feed system according to the speed of rotation of the chipper disc and consequently of its workload.
Models for any requirement
For managing woody material from urban greenery, i.e., from the maintenance of parks, gardens, tree-lined avenues and condominium areas, or even small- to medium-sized woody material, chippers equipped with discs with radial knives are more suitable.
These models have typical working capacities of 10-20 m³/h and maximum diameters of 100-300 mm, with manual loading of the material to be chipped. This is why the feeding mouth is wide, to obviate without difficulty the shredding of the small-diameter but very crowded, and therefore large-volume, brushwood waste and urban prunings typical of forestry and urban pruning. If the loading is manual, a safety device (often represented by a sensor bar) must always be compulsorily installed to prevent the very dangerous dragging of the operator towards the chopping device in the event that part of his clothing (e.g. a loose belt or the end of a sleeve or leg of his working overalls) becomes entangled in the woody mass initiated to chipping.
The alternative is mechanical loading of the biomass with dedicated equipment, which averts any possibility of accidental contact. After shredding, the flakes are either sent into a gooseneck chute for ejection, to form a pile or for loading into trailers, thanks to the strong air current created by the rotation of the shredding apparatus, often enhanced by a suction fan located immediately downstream.
Wheeled model on rubber tracks
To ensure adequate mobility and operational autonomy even when a chipper of limited productivity is sufficient, Peruzzo of Curtarolo (PD) offers the TB-100 C PRO model in its catalog, which uses an undercarriage with rubber tracks. The machine is equipped with a two-blade rotor that can chop material up to 11 cm in diameter and a hydraulically driven feed roller; productivity varies between 4 and 10 m³/h, depending on the type of lumber.
The power source is a 23-Hp gasoline engine, exclusively dedicated to driving the working parts. Instead, the vehicle's advance is provided by a second endothermic engine, with 5 Hp of power, connected to a mechanical gearbox with 3 forward plus reverse gears.
With an overall width of only 76 cm, the vehicle is quite agile for profitable use in tight spaces or terraces and easily loaded onto a van for transfers.
With the addition of a 450 kg capacity platform, the undercarriage can be transformed into a useful wheelbarrow for transporting wood and various materials.
“No-stress” and “no-block”
Rotating at speeds of several hundred revolutions per minute, it is essential that the chopping rotor, whatever type it is, be dynamically balanced very accurately to avoid vibrations that are very detrimental to the life of the device. Moreover, it is increasingly common to install the "no-stress" device. This is a fully programmable electronic device which, depending on the speed of rotation of the working organ, automatically adjusts hydraulically the timber feed rate thus the amount of material to be shredded. As soon as there is a small decrease in the rotation speed due to incipient overloading, the feed rate is slowed down to keep the rotor in the optimal operating condition constantly. In a complementary way, the "No-block" ensures smoothness and continuity to the incoming material flow, intervening in case of accidental blockage of the feeding parts, i.e., the roller (or pair of rollers) and the chain base belt. An hour meter is often installed to ascertain the correct maintenance intervals, ordinary and extraordinary.
The chopping organs: drum or disc
In both cases, sharp knives fixed on a drum or disk rotating at high angular speeds provide for flake formation. Cutting is done by contrasting the knife with a fixed counter-knife. The choice of the best option (drum or disc rotor) depends basically on the compactness of the wood to be shredded, the average diameter and the water content.
The cutting organ is undoubtedly the most stressed during chipping, so sharpening of the knives and their replacement in case of complete wear and tear are operations to be carried out rather frequently. For this reason, all chipping machines provide easy and immediate access to the working tools, for maximum simplicity and timeliness of maintenance.