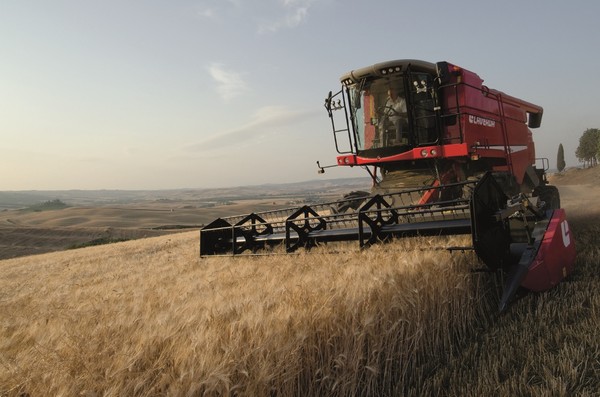
Mietitrebbie: le innovazioni per una raccolta sostenibile
Coniugare produttività oraria e una trebbiatura di qualità rimane uno dei principali obiettivi da parte dei costruttori, ma la necessità di rendere l'operazione di raccolta sempre più sostenibile a livello agronomico ha aperto a importanti evoluzioni tecniche anche nella gestione del residuo colturale e del compattamento del terreno
Nel settore delle macchine da raccolta, uno dei principali obiettivi perseguiti negli ultimi anni dai costruttori è stato quello di coniugare importanti parametri economico-gestionali, come la produttività oraria, con aspetti operativi di tipo “qualitativo” tali da garantire una perfetta estrazione e pulizia della granella contribuendo di fatto all’ottenimento di un prodotto finale fisicamente integro e maggiormente tutelato dal punto di vista qualitativo-sanitario.
L’importante apertura all’elettronica e alla sensoristica nella gestione delle macchine da raccolta ha certamente contribuito a facilitare il raggiungimento di tale obiettivo; tuttavia, tali applicazioni hanno permesso anche di migliorare importanti aspetti tecnico-agronomici conseguenti alle operazioni di raccolta come la gestione del residuo colturale e il compattamento del terreno.
Obiettivo produttività e qualità
La sensoristica nel settore delle macchine da raccolta ha assunto sempre più un ruolo importante nella gestione operativa, in quanto dà la possibilità di intervenire in modo manuale o talora completamente automatico sui principali parametri di lavoro, dalle prime fasi di taglio fino a quelle di pulizia e scarico del prodotto. L’applicazione di sensori, in particolar modo nei punti funzionali più critici e che richiedono frequenti regolazioni a seconda delle diverse condizioni di raccolta del prodotto, permettono quindi all’operatore di non penalizzare la produttività oraria ma al tempo stesso di mantenere trebbiature di elevato standard qualitativo.
Già a livello della testata, rispetto a qualche anno fa è possibile regolare in modo puntuale e, direttamente della cabina di guida, ogni singolo componente funzionale arrivando anche alla possibilità di adeguare in modo automatico la velocità di rotazione dell’aspo abbattitore a quella di avanzamento della mietitrebbia. Importante risulta essere anche la presenza di sensori di ausilio alla guida che, utilizzando segnali DGPS (Differential Global Positioning System) o sensori di contatto o optoelettronici posizionati ai lati della testata stessa, sono in grado di garantire l’afflusso di prodotto sull’intera larghezza di lavoro e al tempo stesso agevolare una più precisa registrazione dei parametri di raccolta.
Recenti sviluppi hanno coinvolto anche il canale di alimentazione. Infatti, l’introduzione di sensori in grado di controllare in continuo il flusso in entrata di prodotto permette di “autoregolare” la velocità di avanzamento in funzione del carico presente, ottimizzando cosi la qualità della trebbiatura e riducendo il rischio di ingolfamenti. Nei sistemi di trebbiatura convenzionale, recentemente è stato introdotto anche un sistema di variazione automatica della velocità degli scuotipaglia in base alla pendenza della superficie. In condizioni di salita, infatti, la velocità degli scuotipaglia diminuisce per ridurre la velocità di trasporto della paglia sugli scuotipaglia, mentre procedendo in discesa la velocità operativa degli scuotipaglia aumenta per evitare possibili intasamenti. La possibilità di regolare automaticamente la velocità degli scuotipaglia al variare delle condizioni di raccolta garantisce una migliore separazione e aumenta la produttività oraria.
È evidente quindi come la possibilità di avere una continua integrazione di informazioni legate al monitoraggio di più apparati di lavoro consenta oggi di poter intervenire in modo continuo sulle singole componenti, in modo tale da impartire regolazioni istantanee sulle base delle reali condizioni operative con positive ripercussioni sulle performance della macchina. Per questo motivo si stanno sempre più affermando sistemi di gestione automatica in grado di autoregolare in continuo importanti aree di lavoro, come ad esempio la separazione della granella, agendo direttamente sui principali parametri che ne definiscono l’operatività ovvero il numero di giri del rotore, il sistema di pulitura, adeguando il numero di giri del ventilatore, e l’apertura dei crivelli a seconda delle reali condizioni del prodotto da raccogliere.
A supporto di tali evoluzioni anche i sistemi di valutazione della separazione della granella sono oggetto di costante attenzione da parte dei costruttori. Recenti innovazioni per la valutazione della qualità di separazione della granella e la determinazione della quota di rotture prevedono l’utilizzo di fotocamere a colori posizionate in cima al canale elevatore. Queste fotocamere, a intervalli di tempo dell’ordine dei secondi, scattano un’istantanea ad alta definizione che sarà valutata da un software dedicato in grado di calcolare le componenti diverse dalla granella come paglia, pula o corpi estranei, nonché la proporzione di granella rotta. I valori interpretati vengono poi visualizzati sul terminale di controllo sia in formato grafico che come immagine reale e qualora si oltrepassi i limiti dei valori impostati l’operatore riceve un allarme visivo.
La gestione del residuo
La fase di raccolta rappresenta anche una delle operazioni colturali più importanti dal un punto di vista agronomico grazie alla possibilità di gestire il residuo colturale in funzione degli obiettivi aziendali. In questi ultimi anni, la gestione del residuo ha assunto sempre più un ruolo di primaria importanza grazie alla larga diffusione di impianti per la produzione di bioenergie ma anche per il crescente interesse relativo all’adozione, da parte delle aziende agricole italiane, di tecniche di lavorazione del terreno alternative alla convenzionale tecnica basata sull’aratura e successivi interventi preparatori.
La corretta adozione di queste tecniche “semplificate” richiede però che tutto il residuo colturale derivante dalle operazioni di raccolta della coltura precedente venga trinciato e distribuito in modo omogeneo su tutto il fronte di lavoro della mietitrebbia in modo tale da avere una velocità di degradazione uniforme e, al tempo stesso, non andare a influenzare negativamente le successive operazioni di lavorazione/semina. Tali necessità hanno spinto i costruttori a lavorare in modo importante sui sistemi di distribuzione dei residui (arrivando a gestire direttamente dal sistema gestionale di bordo la larghezza di spargimento) e sulla regolazione della sovrapposizione centrale, arrivando fino ad un vero e proprio sistema di adeguamento automatico della direzione di lancio in funzione dell’intensità del vento laterale o della pendenza della superficie. Quest’ultima soluzione, resa possibile dalla presenza di due sensori elettromeccanici installati sul retro della mietitrebbia, permette di rilevare l’intensità del vento laterale e l’eventuale pendenza di lavoro, e compesare la direzione di lancio del materiale trinciato agendo sui deflettori in modo tale da avere una distribuzione uniforme su tutto il fronte di lavoro della mietitrebbia.
La maggiore attenzione nei confronti del residuo colturale ha visto anche la possibilità da parte dei costruttori di implementare specifici dispositivi direttamente sulla testata da raccolta. Recenti innovazioni hanno visto il posizionamento di rulli di taglio posteriormente alla testata, in grado di aggredire la biomassa basale della coltura e di fatto aumentare le performance della mietitrebbia in quanto potrà procedere ad una maggiore altezza di taglio rispetto ad una testata convenzionale.
Infine, per quanto riguarda la gestione del residuo per utilizzi bioenergetici, recenti innovazioni prevedono la possibilità di eseguire, contemporaneamente alla raccolta, la trinciatura dei residui colturali e la messa in andana mediante appositi deflettori posizionati sotto la testata agevolando cosi la successiva fase di raccolta della biomassa.
L’attenzione al compattamento
Se in passato non era considerato come una vera e propria problematica, negli ultimi anni, l’interesse dei costruttori nella ricerca di possibili soluzioni in grado di attenuare gli effetti del compattamento del terreno si è fatto notevolmente più concreto. La riduzione delle masse, principale elemento in grado di limitare all’origine il problema del compattamento, non appare di facile modifica in quanto esiste molto spesso una stretta correlazione tra massa e capacità di lavoro, mentre di più agevole attuazione, almeno dal punto di vista tecnico, è la possibilità di aumentare la superficie di contatto tra gli organi di propulsione e il terreno attraverso l’impiego di cingolature o pneumatici larghi e a bassa pressione. Tuttavia, si stanno sempre più diffondendo sistemi di controllo automatico della pressione di gonfiaggio degli pneumatici (non solo per l’assale anteriore ma anche per il posteriore) controllabili direttamente dal sistema gestionale di bordo. Tali sistemi hanno sostanzialmente lo scopo di gestire in modo ottimale i parametri del pneumatico a seconda delle condizioni di lavoro in cui opera la mietitrebbia; in campo, una riduzione della pressione aumenta la superficie di contatto e la capacità di trazione; in fase di trasporto un pneumatico dotato di una maggiore pressione riduce la resistenza al rotolamento e quindi l’usura e i consumi, migliorando al contempo anche la stabilità di guida.