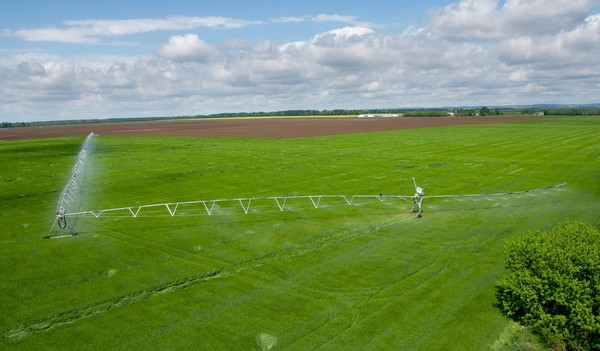
Water for agricolture, a technological challenge
Water is not an unlimited resource so its use must be rationalized even in settings in which its availability has never been a problem. Daily consumption, measured with a "water footprint" method, can be reduced by using increasingly more sophisticated and specific systems for various types of crops
The definition of the water footprint thus involves a sequence of quantity and location of the footprint of a product or process, the evaluation of environmental, social and economic sustainability and identifying a strategy for reduction.
Global computation of the water footprint is provided by the sum of three components which refer figuratively to colors. The blue water is surface or underground water drawn and used for agricultural, domestic and industrial purposes. The green water is rainfall which does not add to surface streams or brooks. The gray water is water required to dilute polluting substances in quantities needed to restore water to the established quality standard.
In this connection, it appears evident that the world of agriculture is strongly involved in all the components of the water footprint. As a result, irrigation technicians and the manufacturers of equipment for carrying out irrigation have been at work for some time on optimizing the distribution of water for the purpose of increasing the efficiency of using it for crops by limiting loss and waste.
The machines
Where it is necessary to integrate irrigation and a water regime for full field crops, the technique is evolving toward the more or less generalized use of hose reel irrigators, commonly known as “big reel” because of the typically huge reel formed as the hose is wrapped when the irrigator is moved in the field. What differentiates the hose reel is the adequator unit which can vary according to the specific purpose of the irrigation operation. In general terms, the most common types are lance and sprinkler booms.
The recent trend of hose reel irrigation has been aimed at savings in manpower, energy and water and attempts to optimize performance.
Uniformity of distribution
Thirty or forty years ago irrigators coupled with hose reels rolled with an impact mechanism which generated a characteristic bell curve causing considerable excess distribution in the center of the strip irrigated with uniformity of no greater than 70-80%. Changes made to turbine irrigators fifteen to twenty-five years ago led to the substantial improvement in distribution, 85-90%, with remarkable results for reducing excess irrigation. Recently, the introduction of variation of the speed of movement allowed a further improvement in uniformity, up to 95-98%, resulting in better adequator rationalization. In practice, the transverse movement of the irrigator gradually increases on the side toward the center of the field to then diminish on a spectacular way on the other extremity. Moreover, to ensure the best uniformity longitudinally, synchronized gears are often used to continuously vary the wrapping of the host in relation to the diameter of the reel. There is no doubt, however, that irrigation booms guarantee a better irrigation uniformity (98-100%) at limited energy costs, also in windy areas and for sensitive crops such as vegetables. Recent models of irrigation booms work in combination with all types of hose reels and operate correctly even with very low working pressure (at only 1.5 bar).
Reduction of manpower
As in other agricultural sectors, in irrigation the need to increase the productivity of workers is very strongly felt. Generally, equipping the reel with servomechanisms and hydraulic transit has made it possible for a single worker to manage wrapping of the hose, also remotely with radio control, for example, for lifting the irrigator trolley and/or the irrigator nozzle bars when they have to be moved, the swivel supporting the reel to anchor and place the equipment, to place the suction pipe head on models equipped with a motor pump.
Water savings
Other than improving the uniformity of distribution, which is undoubtedly a fundamental boost for rationalizing the use of water resources, this is helped by precise and ongoing pluviometer control and programmable CPUs very often equipped with GPS devices for variable interval irrigation based on prescription maps created previously.
The evolution of CPUs for equipping irrigators – powered independently by low voltage rechargeable batteries as well as by photovoltaic solar panels – has decidedly optimized operations in the field. With dedicated software, beginning with the technical characteristics of the irrigator and possibly motor pumps run remotely via wireless transmissions, the farmer can feed in the best rain gauge and distribution uniformity settings for watering the crop, establish, for example, the times to begin and end irrigation, the locations for beginning and stopping the course to guarantee satisfactory water uniformity across the entire field, counts of the length of unrolled and rolled hose as well as the time remaining for completing the operation. Also in this sector, the new frontier is precision farming starting with maps created previously to take into account crop variables, the topographic and pedological characteristics and, with georeferencing of the irrigation features, it is possible to set variable interval irrigation geared to obtaining considerable savings in management while improving the productivity of operations. As regards irrigation terms, maximum versatility with the lance can be achieved by replacing the nozzles to break up the flow of water to adapt it to the soil and the crop. If a speed turbine with velocity which can be regulated, the uniformity of watering can be ensured. On the other hand, the advantage of sprinkler booms and irrigator nozzle bars are not to be ignored for their low pressure operation with energy savings of up to 50% compared to the long distance jet of the lance. In fact, new booms built in galvanized steel or aluminum are capable of covering up to 50 m per transit while achieving an excellent spray of the water.
Energy savings
The evolution of turbine models and large diameter hoses, with the advantage of lowering viscosity wear, recently put to use have resulted in drastically reducing pressure of operations for a tangible saving of energy. Some manufactures, Ferbo, Idrofoglia, RM and others, mount turbines in aluminum alloy flanged directly on the oil bath gear box.
The new hoses in medium-density polyethylene are ideal for trouble-free coping with functions causing significant mechanical stress when winding and unwinding. Moreover, their large diameter of up to 150 mm and great length available, of more than 800 m, greatly extends irrigation productivity by covering crop areas well over 10 ha/day.
The self-cleaning filter which requires no outside power
Orma in Giardino di Imola, near Bologna, has developed the Ekofiltro, the only innovative automatic self-cleaning screen filter working with the hydraulic turbine which uses water pressure to clean itself and needs no electricity or batteries for working.
Ekofiltro is ideal for irrigation operations drawing water directly from canals, marshes, lakes and the like when suction can easily bring up impurities potentially causing damage to the irrigator components. Impurities are discharged periodically, at intervals decided by the end-user, by the use of the appropriate valve located below the device. In practice, the flow of water entering (up to 100 m³/h), which can be regulated by a by-pass, creates a vortex inside the turbine and the rotation of the filter screen, in stainless steel AISI 304 - 120 Micron ©, inside the hot-dipped galvanized tank leaving impurities in suspension and allowing the clean water to pass through.
Screen washing is constant during the filtration by an appropriate series of holes covering totally the surface during the rotation of the circular screen. The removal of impurities happens periodically by means of the appropriate valve. A safety valve ensures a continuous check of the inside pressure to the tank and discharge in case of pressure increase. Operating pressure varies from 4 to 9 bar and the stainless steel filter has a filtering grade of 120-140 mesh.
Irrigate and cooling
RM in Sissa Trecasaali, near Parma, offers for some of its hose reel irrigators mounting internal combustion engines the CWM (Cooling Water Motor) as optional equipment which makes it possible to dissipate heat accumulated by cooling water to lower the temperature of the air issued by the turbo compressor and to use it for irrigation through efficient liquid-liquid exchange. The method makes the traditional radiator and fan totally superfluous.
The elimination of this mass automatically solves the burden of periodic cleaning to make certain that the engine does not stop running because of clogging materials taken in with dust and insects in day and night operations.
Moreover, the elimination of the cooling fan reduces fuel consumption, by up to 10% according to RM, and drastically lowers noise pollution during operations.