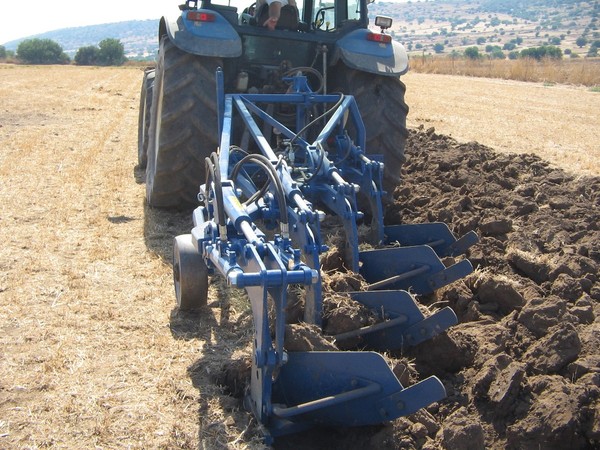
New technologies for open field ploughing
At first glance, the classic mouldboard plough looks like a very simple instrument whereas it is actually one of the implements which has benefited from most innovations over time to reach the point of being designed by modeling software to become a highly sophisticated tool
The plough has been the tool which has allowed man since antiquity to work the ground for successive operations and breaking up the soil. It is almost certain that the first instruments for carrying out these operations were introduced in Mesopotamia thanks to the fact that this is where oxen were trained as draft animals to become available for great traction work. The tools were very simple ploughs teethed with nails, made entirely in wood and capable only of scratching the surface of the soil. Then, however, the Romans, who brought innovations to metallurgy, introduced substantial modifications such as the wheel to facilitate heavy work in the fields, the coulter or knife for vertical cuts of the soil, the ploughshare for horizontal cuts and finally the mouldboard to turn up the clods in the soil.
This configuration remained more or less unchanged until the time of the industrial revolution with the production and spread of ploughs built entirely in metal. In the middle of the nineteenth century came the application of mathematic studies to improve the function of the plough, thanks to the arrival of locomobile power and the multi-share balance plough. Though in England all ploughs were built with metalwork bodies by the end of the nineteenth century, bodies in wood prevailed in Italy until World War II.
But beginning in the twentieth century with the spread of the early tractors powered by gasoline engines came the development of many multi-share plough models, whereas the arrival of tractor lifts starting at the end of the war marked the development and spread of reversible or double ploughs. Seen from World War II was the form and functions of ploughs which were modified and perfected to reach the level of the complicated modern implements.
In general, modern trailed ploughs are almost always equipped with wheels and mainly used for farming north of the Alps where classic ploughing is rather superficial, working outside the furrow with fairly powerful tractors. The shallowness of operations makes it possible to achieve elevated operational capabilities thanks to the drawing force ensured by tractors for as many as 15 ploughshares. At the latitudes of Italy the preference is for maximum productivity in the field for a drive for greater depth and classic work in the furrow, rarely arriving at the use of 5 or 6 ploughshares. The introduction of models which feature folding frames came in very handy for Italian land because they facilitate road transport, whereas the classic mounted models with fixed frame and 3 or more ploughshares carry a risk of exceeding beyond the width which often becomes a certainty. There are also mounted multi-share reversible ploughs equipped with wheels for control of the depth of work which can plough in or out of the furrow mounted on a special frame with advanced parallelogram articulation for self-alignment operated with hydraulics for regulation also during operations.
Technical and agronomic requirements have led over the years to the creation of such special ploughs as balance plows, two plows totally joined at their anterior extremities to the buri, or frame parts, for work on the right and left for overturning slices, always on the same side, digger ploughs for digging ditches and various types of subsoiler plows used for opening the ground for underground channels to clear away excess water.
Whatever the construction of modern ploughs they must feature the characteristics of great strength, lightweight, versatility, maneuverability, quality and work capacity. These results have been achieved through ongoing improvements in the quality of the product based on the past experience of various manufacturers who now use steel qualities with very different characteristics for turning out each single component.
To enable ploughs to work even the most difficult terrain involving cracks, big buried roots and masses under the surface, back in 1870 work began in Australia for developing safety devices thanks to which the body of tools was left free to move up once a certain degree of resistance to torque was reached to be able to follow the path of the obstacle encountered and then automatically relocate on the ground back to work position. This system, now called the non-stop, has evolved from the original creation which featured a spring to become present day hydraulically operated mechanisms which can be modified at will according to the value of the intervention as well.
Also raised over the years has been the level of innovations introduced for such fundamental components as the mouldboards, discissor and tilt parts which today are strongly differentiated as regards shape, often very different, as well as the materials used for the purpose of limiting wear caused by displaced earth to the point of building shares coated with Teflon or plastic materials.
Also the bure, which is actually nothing other than the plough frame, has benefited from the technology evolution which has increasingly over time strengthened its rigidity and structural resistance without proportional increases in weight. To achieve these results there has often been recourse to software for modeling the solid states of the finished components allowing the design stage to include all the calculations necessary for understanding the force of the resistance of all points of the implements during operations for optimizing it already at this stage before applying numeric control to the successive stages of the manufacture of the plough to guarantee maximum precision and quality. There is also research on many prime materials, prized materials with resistance characteristics to counter elevated weakening in normal use in the field. All this for allowing some manufacturers to produce their own special steel to achieve exclusive production.
The technological evolution in the field of metallurgy has made greatly researched boron and microally steels available for the construction of such cutting tools as coulters, shares and share fronts now guaranteed for much longer lifespans that those made decades ago.
Though the world leader in this field is the Norwegian Kverneland, now a part of the Kubota Group, there are a multitude of companies in Italy specialized in the manufacture of plows, companies with medium capacities for the production of extremely high quality implements which have allowed them to export more than 90^ of their production. There are also artisan enterprises, working as ateliers tailoring single products for special ploughs for special local needs such as extremely tough terrain or ploughing to extreme depths. Without any claim to providing complete coverage of the issue in light of the large number of Italian brand names, it is however worthwhile to cite a few of the most well known for information abroad. Amongthem are Nardi in Perugia, Moro Aratri in Fontanella (Bergamo), the Venitian Moro Pietro Meccanica, Annovi Aldo & C. in Modena, ER.MO. In Cremona, C.M.A. in Predappio, Greco Fratelli in Mantua, Colia Meccanica in Foggia, Emmegiemmein Brescia, Di Raimondo and SIDER.MAN in Sicily, aswellasBordin Ettore & figli. In Padua.