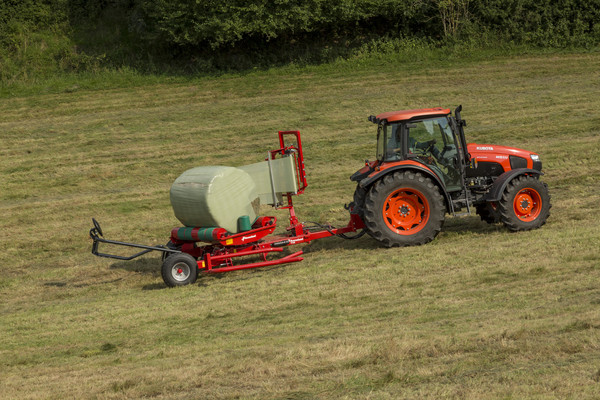
Semi-hayed forage wrappers
Compared to traditional haymaking, the wrapping of semi-wilted forage bales effectively creates mini-silos, with several advantages regarding the quantity and quality of the product. The wrapping machines on the market today offer various alternatives for carrying out this routine, including the simultaneous packing and wrapping, in many cases with a high degree of automation
The wrapping of semi-wilted forage bales has long been a valid alternative to traditional haymaking, with the fundamental advantage of being able to harvest and then store the product even in uncertain or unfavourable weather conditions. Among other things, with this solution the losses are considerably reduced, thanks to the limited handling of the product, greatly benefitting its nutritional content.
To obtain good results, however, it is important to mow the grass at a minimum of 6-7 cm in height, to avoid polluting it with the soil, which carries clostridi spores, and to harvest at a correct humidity level, generally 30-40% for grasses and 50-60% for legumes.
The success of the mini-silo (which the wrapped bale can be considered to be) requires some precautions: ensuring a high volume of the product, obtained with high strength pressing machines, as well as achieving a proper degree of pre-stretching of the plastic film, usually about 50-60%, in order to ensure a good adherence to the round bale, together with an acceptable reduction in the height of the film (typically between 5 and 10 cm) and a minimal decrease in its thickness. Insufficient film tensioning results in a wrap that is unsuitable for good storage, while excessive tension causes a risk of perforations, tears and breakages.
The wrapped bale has a further advantage, related to its extremely timely use: thanks to its limited mass, once opened, it is quickly consumed, before the oxygen contained in the air can resume the degenerative aerobic microbial activity.
The so-called “hay-silo” involves slightly higher costs than traditional haymaking, but largely offset by the increase of obtainable forage units (with the same initial harvest), hence with a concurrent decrease in the administration of concentrates to the herd.
The winding technique
The main purpose is obviously to ensure the best insulation for the bale from the outside air, so that usually 4 to 7 layers of plastic film are superimposed for an optimal wrapping. The winding must also be aimed at achieving the best mechanical resistance of the wrapping in the subsequent handling steps, and the most effective escape of the air from the forage mass while the film is being wrapped.
The basic alternatives of the wrapping phase either involve keeping the unwinding film roll fixed while rotating the bale on the two horizontal and vertical axes, or to provide the winder (or the winders) with peripheral movement and rotate the bale only the horizontal axis. Although several simple wrapper models are based on the first solution, clearly the best efficiency of this routine is obtained when they are both moving, and even better if there are two (so-called “satellite”) winders in action, because they work simultaneously in diametrically opposed positions.
If only bale is moving, the rotation in the vertical axis is ensured by the action of the entire support platform, which is then mounted on a central pivot, while the movement on the horizontal axis is achieved by means of 4 or 5 driving belts made of high friction coefficient textile material (or alternatively with 2 or more steel rollers, smooth coated with rubber or ribbed), on which the bale rests. If, on the other hand, the winder or winders are of the satellite type, the bale is moved on the horizontal axis only.
In any case, the adjustment of the peripheral speeds of the two combined drives determines the amount (usually 60-70%) and the geometry of the overlay of the different film layers, according to how they cross over each other.
Options for controlling the routine
The simplest models use a mechanical control of the routine through cables and levers, while the more advanced ones are equipped with a control unit able to complete the winding cycle in a completely automatic way. In this case, the entire operation is controlled from the driver’s seat by means of a joystick mounted on the armrest next to the tractor driver’s seat. For some models, radio remote control is also available on request.
Loading and unloading
An additional, rather important aspect for what concerns work productivity is the movement of the bale as it is and after the wrapping.
The loading can take place in the traditional way, i.e. by lifting and positioning the bale on the wrapping machine with the aid of a tractor equipped with a front loader with forks or claws as end tools (or even with a telescopic handler), or in automatic mode, with bale position detection and the adaptation of the wrapping machine for intercepting the bale.
The unloading must be done with the utmost care, to avoid damaging the plastic film by puncturing it, and to prevent unwanted rolling movements, which are particularly likely on mid-to-high slopes. If the bale support is the rotating platform equipped with belts, this is often what flips towards the back of the machine, in order to “shake” the wrapped bale onto the ground. If, on the other hand, the support base consists of rollers, these are simply progressively widened, sliding on the outer wrapped surface, gently resting the bale on the ground.
Often the same model of wrapping machine is offered in different versions: mounted (to the 3-point linkage of the lifter), semi-towed (with an axle equipped with wide wheels to limit soil compaction), or even in a configuration suitable for fixed point use.
Combined operations
Since wrapping follows the packaging of the semi-wilted forage, maximum productivity is achieved by the simultaneous execution of the two phases of a single routine. Said and done: for some time now several models of wrapping machines have been available with two devices mounted on a single frame, combined to work in close synchrony. It is obviously essential that the time necessary for wrapping the already packaged bale is less than or equal to that of the packaging of the next bale. Particular attention is given to the step of passing the bale from the pressing chamber to the wrapping module, for the best positioning in relation to the subsequent winding phase, which is performed according to the methods illustrated above.
For some models, an alternative option is to arrange the unloading of the round bale on the circumference or on a flat side. The latter solution is more beneficial in cases where the work is carried out on sloping ground and/or in the presence of forage tough stems, because the film on the flat side has a greater resistance to perforation of the layers. To offer maximum operating flexibility, some manufacturers offer wrapping machines that can be combined with any baler.
The plastic film
The basic material is polyethylene (PE), with added isobutyl rubber (to give the film a high elongation capacity) and ethyl vinyl acetate (EVA) for greater mechanical strength. In addition, additives are added for the best protection against UV rays. The external surface of the film is tacky, for a good adhesion to the forage and during the overlapping of the layers, and to provide a sealing effect that is as hermetic as possible. Meanwhile, the internal surface is smooth, to make it easier to unwind the reel.
Moreover, especially if the wrapped bales are left in the field for a long time, a good film must adequately protect the fodder from the effects of ultraviolet rays, to prevent the disruptive action exerted by these harmful radiations. It must also be able to ensure good resistance to atmospheric agents such as frost, rain, snow, wind and temperature fluctuations. The colour also has its importance. To limit the landscape impact from the initial black film, we then moved on to white, and then settled on an excellent “grass green”, which represents a good compromise, also to avoid excessive heating of the mass when the sunshine is intense.
For best adhesion both to the bale and between the different layers, it is important to ensure an adequate pre-stretching of the film, which is obtained by unrolling the film between aluminium rollers. This operation is also useful to avoid the creation of possible irregularities in the film, which can be caused by excessive tension exerted on the material. On most models, roll replacement is automated, making it quick and easy.
System for large square bales
Haymaking productivity has undoubtedly made a great leap forward with the appearance of the “big balers”, that is to say machines that instead of making round bales create large prismatic bales. Basically it is a sort of return to the origins, or the old (but not yet completely outdated...) square bales, with the fundamental difference that in the modern reinterpretation, the size (and therefore the weight) of the bales is much higher.
It should be noted that the gathering and pressing of the forage in prismatic bales is completely different from that of the round bale. For the latter, the product enters by rotating in the compression chamber and is progressively bundled, while in the prismatic packing machines the fodder is introduced rhythmically through large forks in set quantities, to then be pressed with the alternating action of a powerful piston.
Even though the bale formation is different, similarly to the round ones, the large prismatic bales can be fruitfully wrapped with plastic film to create minisilos. In this case, the wrappers are obviously more sturdy, and differ substantially in terms of loading and unloading the bale, sometimes characterized by high automation, whereby the processing can be carried out without interruption, resulting in a particularly high productivity.
The French company Kuhn recently launched, among others, the SW 4014 model, which can handle the entire working routine without any intervention by the operator, also using ISOBus technology and laser sensors for measuring the bale position and size, in order to optimize the wrapping.
The coordinated hydraulic movement of 4 large steel rollers provides for the loading, rotation and unloading of the bale, while two satellite winders wrap the forage with the plastic film.
For hydraulic services, the machine requires a flow rate of only 60 l/min, a requirement that is easily satisfied even by medium-powered tractors. Alternatively, an independent pump, driven by the tractor PTO, is also provided in the ECO mode.